Quels sont les principaux obstacles à l’adoption de technologies d’automatisation et de robotisation des processus?
Tout d’abord, il y a bien sûr la complexité, le manque d’espace et le manque de savoir-faire. Toutefois, les décideurs s’arrêtent souvent au prix de la solution, facteur préoccupant, s’il en est un. Quel est le prix d’un robot collaboratif? On cherchera ici à déboulonner certains mythes ayant trait à l’investissement technologique nécessaire à l’acquisition de robots collaboratifs (cobots) – entre autres en matière de dépenses en immobilisations (CAPEX) et de rentabilisation (ROI).
Qu’est-ce qu’un robot collaboratif?
Vous avez sans doute une bonne idée de ce qu’on entend par « robotique collaborative ». On résumera le concept ainsi : collaborative + robot = cobot.
Là où le robot industriel excelle dans le travail à la chaîne et s’avère très rapide, propre à une tâche spécifique, rigide et souvent massif, le cobot est relativement léger, polyvalent, adaptatif et généralement plus petit que son homologue industriel.
Quel est le prix d’un robot collaboratif? De manière générale, l’acquisition d’un robot collaboratif représente un investissement de l’ordre de 40 000 $ à 70 000 $, mais il s’agit là d’une fourchette de prix à prendre avec un grain de sel. Le point le plus important pour l’acheteur est d’établir la distinction entre le prix du cobot et le prix de la cellule robotisée en entier.
Tout dépendant de la complexité du projet, du réaménagement nécessaire, des ressources déployées en intégration et du processus à automatiser, le coût total peut varier entre 150 000 $ et 250 000 $. En comparaison, l’intégration de robots industriels coûte environ 10 fois plus cher.
Le cobot comme investissement et non comme simple dépense
Il faut dire que le simple fait d’intégrer un cobot dans les activités de l’entreprise ne crée pas et n’ajoute pas de valeur en soi. C’est lorsqu’on le juxtapose et l’adjoint aux composants d’une cellule de production en début, en milieu ou en fin de chaîne que le robot devient un vecteur de productivité. Il faut donc d’abord penser au processus à automatiser. Par opposition aux solutions de robotique industrielle, les cobots sont polyvalents, modulaires et modulables. C’est-à-dire qu’on peut commencer « petit » – en s’assurant que la solution est robuste et qu’elle apporte de la valeur – avant d’automatiser d’autres segments de la chaîne de production.
Par exemple, l’achat d’un cobot sans plan d’intégration établi en amont pourrait s’avérer non productif et non rentable longtemps. L’intégration éventuelle se traduira par beaucoup d’essai-erreur et de gaspillage de ressources (d’argent, entre autres).
Un cobot peut seulement être qualifié d’investissement lorsqu’il crée ou ajoute de la valeur – et cela se mesure de différentes façons :
- Réaffectation du personnel à des tâches à valeur ajoutée
- Augmentation de la capacité de production
- Réduction du nombre de blessures
- Augmentation de la qualité des extrants
- Ajout d’un ou de plusieurs quarts de travail
- Accroissement de la précision et de la répétabilité
Lorsqu’on parle de plan d’intégration, on fait surtout référence aux composants matériels, aux ressources humaines et au temps nécessaires à la mise en marche initiale de la cellule robotisée. Ces éléments s’inscrivent dans les dépenses d’investissement (CAPEX).
- Robot collaboratif
- Base ou support de robot
- Outils effecteurs (préhenseur, visseuse, etc.)
- Dispositif d’alimentation en pièces (convoyeur, chute, etc.)
- Dispositif de référencement (système de vision, signaux d’entrée-sortie, etc.)
- Autres composants matériels (capteurs, relais, alimentation en air comprimé, etc.)
- Autres composants logiciels
- Dispositifs de sécurité
- Ressources en intégration (internes ou externes)
Exemple de ce à quoi il faut penser
Prenons l’exemple d’une cellule de palettisation. On y trouvera un robot, des capteurs de boîte, des capteurs de palette, des rideaux lumineux ou des scanners de surface, un ou plusieurs préhenseurs choisis selon la charge à palettiser, un dispositif d’apport en air comprimé, s’il y a lieu, un convoyeur, un système d’interfaçage, de câblage et de communication faisant interagir les composants de la cellule, un logiciel de palettisation, et bien plus encore. S’ajouteront à cela les ressources en intégration.
Évitons-nous donc certaines surprises : le coût de la cellule en entier peut coûter de deux à six fois plus cher que le robot en tant que tel.
Sachez qu’il est possible de contourner les CAPEX liées au robot en profitant d’options de financement offertes par certains fabricants. Les PME y trouvent souvent leur compte étant donné leurs moyens financiers restreints et les fluctuations importantes de leurs flux de trésorerie.
Rentabilisation de l’investissement
Il faut dire que l’utilisation intensive d’un cobot dans le cadre d’une cellule robotisée doit évidemment permettre à l’acquéreur de « rentrer dans son argent », c’est-à-dire d’atteindre le seuil de rentabilité – terme à ne pas confondre avec la rentabilisation de l’investissement (return on investment, ou ROI)..
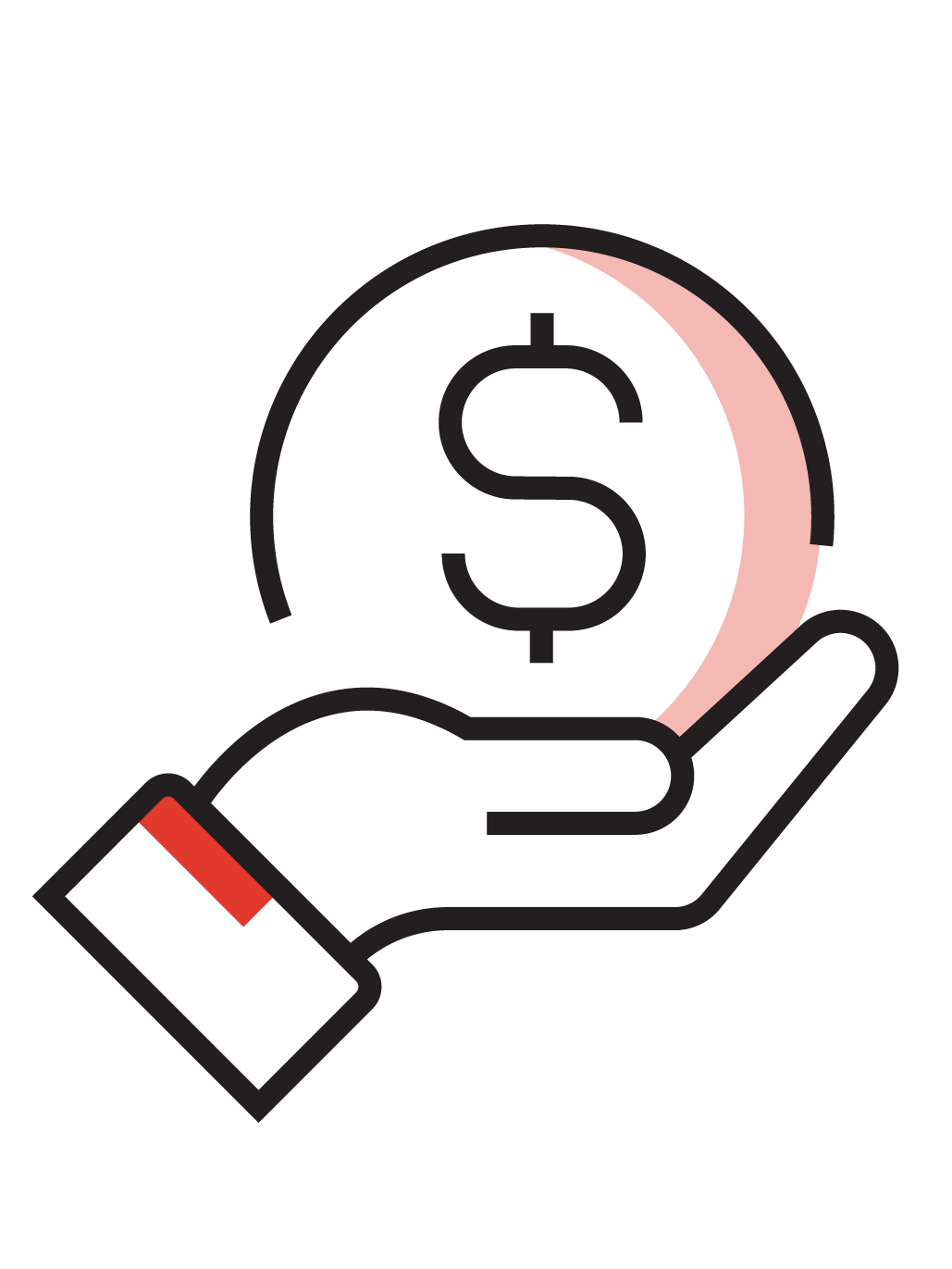
Les économies en salaire, l’ajout d’un quart de travail, la réduction de la quantité de matières premières requises, les dépenses en électricité, l’augmentation du nombre de pièces traitées, la réduction du nombre d’erreurs et de pièces défaillantes… Tous ces aspects entrent en ligne de compte dans le calcul du ROI. Par exemple, après une période donnée – disons un an – un cobot coûtant 50 000 $ aura permis de dégager des économies de 20 000 $ (ayant soustrait les dépenses qu’occasionne le robot des revenus qu’il permet de générer). Pour cette année, le robot aura atteint un ROI annuel de 40 %.
En bref, il suffira d’étendre ce concept à l’échelle de la cellule robotisée pour avoir une bonne idée du moment auquel le seuil de rentabilité sera véritablement atteint, et des économies réelles que génère l’intégration d’un robot dans une chaîne de production.
L’importance de la simplicité d’utilisation
N’oublions pas les impondérables, soit les besoins en programmation et en reprogrammation. La solution robotique devrait être adaptative. Il existe un grand nombre d’événements qui peuvent nécessiter des efforts en programmation – pensons seulement aux changements de produits, aux changements d’outils, aux changements de spécifications des matières à traiter, à l’ajout d’une étape au processus, à la réaffectation du robot à une autre étape de la chaîne de production et bien plus. C’est pourquoi il est très important de se doter d’une solution intuitive et facile à apprendre, et de se concentrer sur le développement des connaissances robotiques à l’interne afin d’alléger le fardeau des dépenses d’exploitation.
Puis il y a le coût de renonciation. On peut illustrer ce concept de différentes façons, mais la plus évocatrice est de se représenter les conséquences d’un refus de changer ses pratiques industrielles. En dessinant deux scénarios futurs, un avec un robot et l’autre sans robot, on peut évaluer combien il en coûterait de renoncer à l’acquisition et à l’intégration. Il faut alors prendre en considération les aléas du marché, les fluctuations et conjonctures économiques, la crise de la main-d’œuvre, l’accélération du développement technologique, le dynamisme de la concurrence, etc. On se rend alors compte que le simple fait d’attendre deux ans avant d’entamer une démarche d’automatisation peut se traduire par un grand retard dans la course technologique, et des dizaines, sinon des centaines de milliers de dollars en perte de revenus éventuels à moyen terme.
Finalement, quel est le prix d’un robot collaboratif et combien pourrait coûter votre projet d’automatisation? Avez-vous pris tous les aspects essentiels en considération? Dans le doute, demandez à un expert de chez Automatisation Pneumac de faire le calcul avec vous!