Applications for collaborative robots that
adapt to your industry
Robots - especially collaborative ones - are an excellent starting point for automating manufacturing processes.
For manufacturers, the following tasks are among the most frequently and easily automated processes:
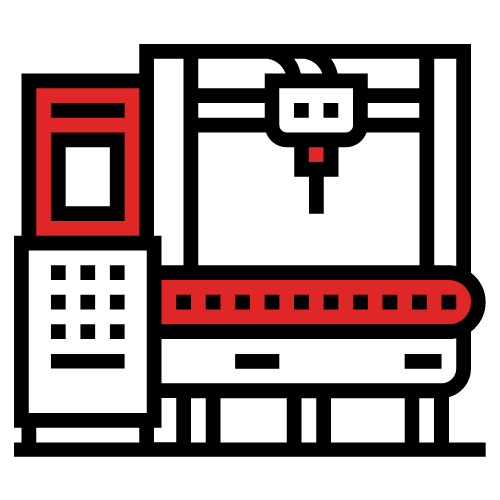
Machine Feeding and Machining
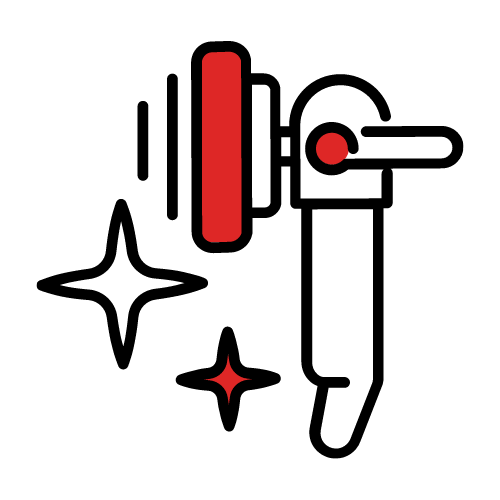
Finishing, Deburring, Polishing
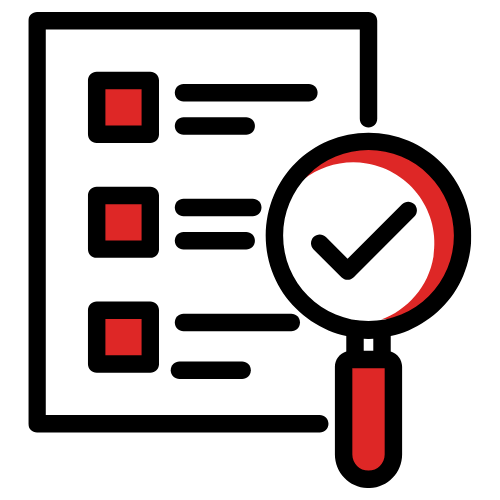
Inspection and quality control
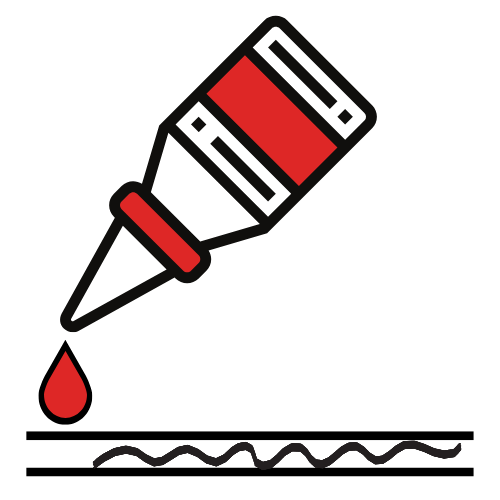
Removal of adhesives and other materials
Process automation of all kinds is just around the corner in many industries. Some manufacturing sectors have welcomed or are welcoming robotization with open arms, while others are waiting for the most opportune moment, which can take many forms:
-
-
Assessing the company's financial health
-
Lack of manpower
-
Increased demand (potential productivity gains)
-
Increased safety risks
-
At Automatisation Pneumac, we have in-depth knowledge of Universal Robots (UR)(UR) robots, and have great confidence in this brand's products.
First and foremost, UR cobots are the most widely used in the worldand with good reason! They are known for their unrivalled versatility and ability to adapt to a wide range of industries. Whether used at the beginning, middle or end of a production line, or even to carry out a series of manipulations at a single workstation, UR robots have everything it takes to facilitate the migration towards digitization of business activities.
Tasks and processes that can be automated with collaborative robots
Assembly
Assembly can involve a variety of processes, including screwing, mounting, fastening, connecting and other handling tasks for parts and sub-assemblies. By performing various manipulations such as transferring and inserting objects, a collaborative robot can quickly and accurately assemble parts. These include mechanical, pneumatic and electronic assemblies.
Palletizing
Palletizing involves stacking loads on different trays or other loading devices for storage or transportation.
When equipped with end-effectors compatible with the loads to be palletized, cobots can perform this task, which is often a source of injury, material damage, forgetfulness and other factors with negative consequences for productivity. Compatibility between end effector and load to be palletized depends, among other things, on the material, porosity, mass and size of the materials to be handled.
The ability of collaborative robots to perform repetitive and precise tasks is a clear demonstration of their usefulness in such a process.
Welding
Welding tasks are many and varied, and can be found in a wide range of industries (electronic components, joining assembly parts with weld beads, equipment maintenance, additive manufacturing, etc.). Of course, some types of welding lend themselves better to automation.
The advantages of automating this process include repeatability and consistency of welds, low wastage of fusible electrodes (consumables), little reprocessing and rework, and rapid arrival of processed units on the market.
Screws
Generally considered a sub-task of assembly, screwing is a very common task on production lines. Once again, since they are generally equipped with torque and force control functions, cobots enable screwing to be carried out with unrivalled precision. Since the parameters are exactly the same for a given task, the process is reliable and the results consistent. When it comes to compatibility, everything depends on the screwdriving end effector used and the fastening elements employed.
Machine feeding and machining
Although the official equivalence of the term machine tending is "machine monitoring", it's more a question offeeding, loading and unloading machines. We're talking here about lathes, milling machines and other CNC machining equipment. Rather than employing one or more workers to keep these machines running continuously, manufacturers today have access to a number of robotic solutions to perform a range of repetitive tasks.
- Opening the machine door
- Loading and positioning of raw parts
- Actuating the clamping device
- Closing the machine door
- Machine start-up
- Reopening the machine door
- Unloading the machined part
- Cleaning of machine and clamping device, if necessary
- Reading signals (vision system, input/output, robot program)
Finishing, deburring, polishing
These surface treatment processes often depend on qualities that are difficult to achieve by manual workers, even when equipped with task-specific power tools: uniformity, consistency and repeatability. Given their quarter-turn adjustable programmingprogramming their ability to follow ultra-precise trajectories, taking all axes into consideration and the advantages provided by torque and force control functionsWhen it comes to automating surface treatment, collaborative robots are the obvious choice.
Inspection and quality control
Inspection and quality control tasks are numerous: calibration, sizing, tolerancing, testing of printed circuit boards, chips, tactile functions, buttons, interfaces, and so on. Generally speaking, companies that assign human resources to such repetitive work would benefit from reallocating these people to higher value-added tasks. Cobots, with their logic and signal interpretation, are specially designed for inspection and quality control processes.
Removal of adhesives and other materials
Here's another task that requires exemplary consistency in execution: quantity of material to be deposited, speed of movement and trajectory to be respected. Although manual workers put all their willpower into achieving uniform results, they are generally prone to fatigue, errors, absenteeism and much more. This makes collaborative robots ideal for the repeatable application of semi-liquid substances in a wide range of industries, such as assembly, dispensing and caulking.
Key benefits of collaborative robots
We could list numerous other applications, fields of application and contexts in which cobots are used, all of which underline their great versatility. But we mustn't forget the features that make them the instruments of choice for manufacturing companies: their modular and modular nature, and the fact that they can be used in a wide range of applications. modular and scalabletheir quick paybacktheir numerous integrated safety features and intuitive intuitive programming.
Do you need help getting your automation project off the ground?Aspects such as financing, space planning, configuration, training and machine operation are sometimes difficult to clarify. If so, call on the professionals and experts. Contact the staff at Automatisation Pneumac!
Ready to automate your tasks?
Think you have an interesting project?
Would you like to know more?
Address
100 Goyer Street, room 103
La Prairie (QC)
J5R 5G5
Phone
514.745.1987
1.800.361.1684
info@pneumac.qc.ca