CASE STUDIES
Discover these case studies illustrating innovative solutions in automation, collaborative robotics, pneumatic systems and vacuum lifting. Learn how to optimize productivity, improve efficiency and guarantee safety through real-life applications. Each case study details the challenges faced, the solutions implemented and the results achieved.

Automate virtually anything. Universal Robots robotic arms are used daily in thousands of production environments. Below is a selection of case studies where Universal Robots collaborative robots have been used to automate a variety of production and manufacturing tasks.
DCL Logistics deployed Universal Robots' UR10e cobot to automate picking and packing of items in its fulfillment center. Thisincreased efficiency by 500%, reduced labor costs by 50%, achieved a return on investment in three months, and guaranteed 100% order accuracy.
OptiPro Systems, a manufacturer of precision optical manufacturing equipment, needed to meet a growing demand for automated solutions to measure products during the manufacturing process. They found the solution with an application kit for measuring small parts powered by a Universal Robots UR3 cobot. Quality control is crucial, requiring 100% inspection.
In less than five years, Go Fast Campers (GFC) has gone from an initial concept to an innovative manufacturing operation with 65 employees. A line of fully integrated UR5 cobots uses a single program to produce any part, on any CNC machine. This makes it possible to manufacture high-quality components, while rapidly integrating customer feedback.
Two palletizers powered by Universal Robots and Robotiq are helping Napco Brands in the Chicago area to expand its private label coffee business despite labor shortages, increasing productivity by 15% and reducing the risk of injury while freeing up eight workers a day for more rewarding tasks.
The manufacturer deployed Universal Robots' UR10e cutting cobot at a fraction of the cost and production time of a CNC machine, cutting cutting cutting time by almost half and reducing late shipments to less than 1%, while improving employee safety and growth opportunities.
The Vermont-based manufacturer of wooden tableware has successfully deployed an UR5e collaborative robot to perform the final sanding of cutting boards. The new robot colleague, named 'Sandrew' by the staff,increased production throughput by 40%, enabling the robot to pay for itself in just two months.
The company integrated ten collaborative robots from Universal Robots using only in-house resources. This eliminated additional programming and maintenance costs. The installation was carried out without modifying the existing plant layout, enabling new applications to be configured in less than an hour.
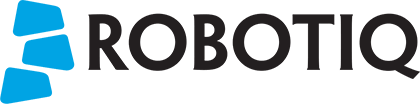
Elevate your workforce with easy-to-use cobot solutions that do the work for you. Robotiq's tools and know-how simplify collaborative robot applications, enabling factories to start production faster.
Robotiq's palletizing solution combined with the UR20, which offered the necessary collaborative solution without the need for safety cages, making it 100% collaborative. Leveraging Robotiq's expertise and team, Nutriset found the ideal automation configuration to efficiently optimize its palletizing process.
Ornua chose a collaborative palletizing solution so that its employees could interact with the product if necessary. It opted for a UR20 with the Robotiq Palletizing Solution to palletize various dairy products and canned dairy products.
Usinatech has accelerated its transition to automation. Patrick Côté and Vincent Roussy proudly report that their transition has resulted in productivity gains, reduced operating costs and low staff turnover. This has stabilized all aspects of production and distribution.
Rather than try to automate everything at once, he started small. And it worked: his Robotiq 2F-140 gripper, mounted on a Universal Robots UR10 robot - itself ceiling-mounted - feeds three separate machines. He is now installing a Robotiq CNC feeder kit on a new UR robot to automate a second process.
Sennheiser now handles 115 different printed circuit boards using Robotiq's 2F-85 adaptive gripper. The number of units tested has risen by 33%. Sennheiser also used Robotiq's Insights software to track daily production. The resulting data justified the addition of a new Universal Robots cobot in summer 2019.