Collaborative robotics, or cobotics, is on the rise in the world of industrial production. Unlike traditional robots, which are often confined to secure environments separate from workers, collaborative robots are designed to interact directly with human operators. This integration of technology and workforce is profoundly transforming production chains, bringing innovations that are redefining manufacturing processes. This article takes an in-depth look at the aspects that make collaborative robots a revolution in modern production chains, highlighting the specific benefits they bring.
Agile response to market needs
One of the major upheavals brought about by collaborative robots in production lines is their ability to respond rapidly to changes in market demand. Traditionally, adjusting a production line for different products or new variants required costly and complex modifications. With collaborative robots, companies can reconfigure their production lines more fluidly and quickly.
Collaborative robots are capable of performing a variety of tasks, and can be reprogrammed for new functions with great speed. For example, in the food industry, a production line can quickly switch from packaging food products to packaging cosmetics simply by changing the robot's parameters. This flexibility enables companies to adapt more effectively to market trends and meet customer demands without major production interruptions.
Increased safety and reduced risk
Safety is a crucial concern in production environments. Collaborative robots bring a new dimension to safety, reducing risks for workers. Designed to work in close proximity to humans, these robots feature advanced sensors and integrated safety systems to ensure safe interaction.
Unlike traditional industrial robots, which often require safety barriers to prevent accidents, collaborative robots can detect the presence of operators and adjust their movements accordingly. This reduces the risk of injury and allows workers to be closer to automated processes, contributing to a safer, more collaborative working environment.
Optimization of logistics and inventory management processes
Collaborative robots are not limited to manufacturing and assembly. They also play a crucial role in inventory management and internal plant logistics. By integrating collaborative robots in these areas, companies can improve the efficiency of logistics operations and reduce the human errors associated with inventory management.
Robots can be used for tasks such as transporting materials, automated storage and inventory management. For example, a collaborative robot can move pallets of finished goods around a warehouse, sorting them according to orders and preparing them for shipment. This automation of logistics processes not only saves time, but also improves the accuracy of inventory management operations.
Improved working conditions and reduced fatigue
Working conditions in production environments can be trying, especially when tasks are repetitive and physically demanding. Collaborative robots provide valuable relief to workers by taking over these arduous tasks, reducing fatigue and the risk of musculoskeletal disorders.
By lightening the physical workload of employees, collaborative robots help to create a more pleasant, less stressful working environment. Workers can concentrate on more interesting and stimulating tasks, which can also improve their satisfaction and commitment to the company.
Enhanced innovation and new product development
Collaborative robots stimulate innovation by enabling companies to explore new approaches to manufacturing and product development. Thanks to their flexibility and ability to be rapidly reconfigured, companies can experiment with new processes and technologies without having to invest heavily in specialized equipment.
For example, a consumer goods company can use collaborative robots to test new product designs and adjust manufacturing processes based on feedback. This ability to innovate rapidly and adapt production processes is a valuable asset in a constantly evolving market.
Reduced training and adaptation costs
Implementing new technologies can often require extensive staff training. Collaborative robots, however, are designed to be intuitive and easy to program, reducing the cost and time involved in training employees. Simple user interfaces and programming tools based on visual concepts enable workers to learn to use the robots quickly and efficiently.
This ease of use facilitates the integration of robots into existing production lines, enabling companies to reap the benefits of robotics without requiring significant investment in training or skills development.
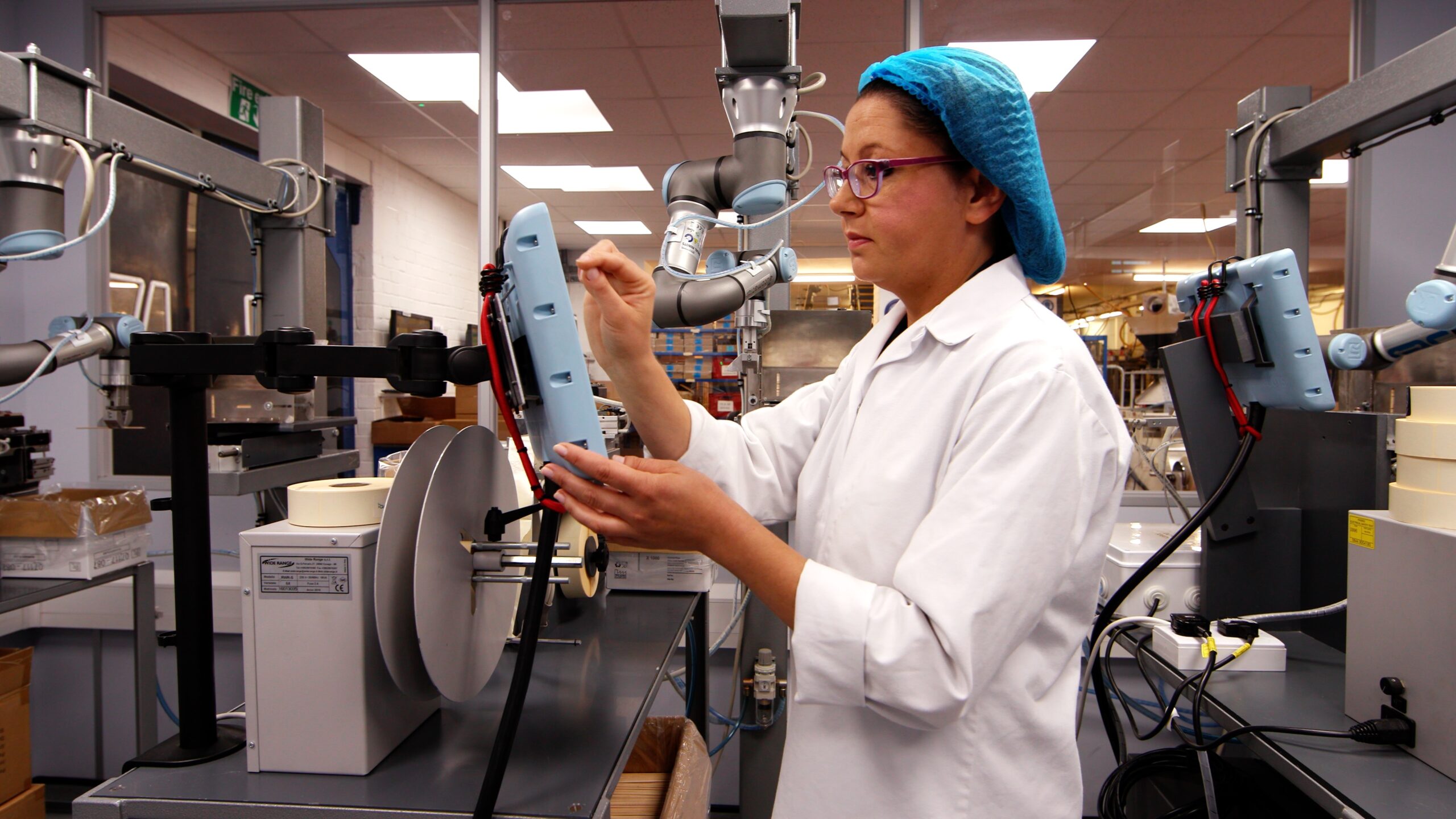
Conclusion
Collaborative robots bring major innovations to modern production lines, improving flexibility, safety, inventory management, working conditions, innovation, and reducing training costs. By integrating these advanced technologies, companies can transform their production operations, respond more effectively to market needs, and create a safer, more pleasant working environment. For companies seeking to remain competitive in an ever-changing world, collaborative robotics represent a strategic opportunity to revolutionize their production chain and achieve new levels of performance and efficiency.
Do you need advice?