A practical guide for companies considering the integration of collaborative robots, with advice on planning, installation and training.
Integrating collaborative robots: best practices and tips
Integrating collaborative robots into a production environment can bring considerable improvements in terms of efficiency, flexibility and quality. However, to take full advantage of these benefits, it is crucial to follow best practices when integrating them. This article explores the key steps and practical advice for successfully integrating collaborative robots into your production chain, maximizing their impact while minimizing potential challenges.
Needs Assessment and Goal Setting
Before integrating a collaborative robot, it's essential to carry out a thorough assessment of your needs and define clear objectives. This involves analyzing your existing production processes, the tasks you wish to automate, and the improvements you hope to achieve.
Advice :
Process Analysis: Identify repetitive, monotonous or physically demanding tasks that could benefit from automation. Assess how the introduction of a collaborative robot could improve these processes.
Objective setting: Set measurable objectives, such as reducing downtime, improving quality or increasing production capacity. These objectives will guide the choice of robot and its integration parameters.
Choosing the right collaborative robot
Choosing the right collaborative robot for your needs is a crucial step. Collaborative robots vary in terms of size, load capacity, reach and functionality. It's important to select a robot that specifically meets your task requirements and the space available in your production environment.
Advice :
Specification evaluation: Make sure that the robot has the load capacity and reach required to perform the intended tasks. Also check compatibility with existing tools and equipment.
Feature Consideration: Some tasks may require specific functions such as machine vision or force detection. Choose a robot that offers the features you need for your applications.
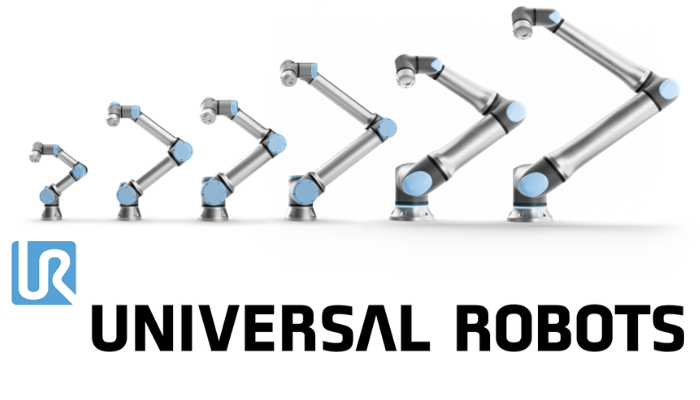
Integration planning
Planning is a key stage in the successful integration of collaborative robots. This phase involves designing the robot's location in the production line, coordinating with existing processes and preparing the necessary resources.
Advice :
Location Design: Determine where the robot will be installed and how it will interact with other equipment and human operators. Prepare the space accordingly to accommodate the robot and allow access to it.
Process coordination: Ensure that the collaborative robot is seamlessly integrated into existing production processes. Avoid disruptions by carefully planning the transition and adjusting processes where necessary.
Employee training and awareness
Employee training is essential to ensure safe and effective use of collaborative robots. Operators need to be trained not only to use the robot, but also to understand how it interacts with their daily tasks.
Advice :
Technical training: Provide operators with in-depth technical training on robot operation, programming and troubleshooting.
Safety awareness: Educate staff on safety protocols specific to collaborative robots. Although these robots are designed to be safe, it's important that employees know the safety procedures and behaviors to adopt.
Robot Programming and Setup
Programming the collaborative robot is a crucial step in ensuring that it performs tasks correctly and efficiently. Most collaborative robots are designed for easy programming, but it's important to get it right to avoid errors and inefficiencies.
Advice :
Use Intuitive Interfaces: Take advantage of the intuitive user interfaces offered by most collaborative robots to configure tasks and movements. Use simulation tools to test programs before implementation.
Adjust Parameters: Set the robot's parameters to optimize its performance according to specific task requirements. Make sure movements are smooth and precise to avoid errors.
Ongoing maintenance and monitoring
After integration, ongoing maintenance and monitoring are essential to ensure that the collaborative robot operates optimally and continues to meet production needs.
Advice :
Maintenance program: Set up a preventive maintenance program to check the robot regularly and make sure it's working properly. Carry out the necessary repairs to avoid production interruptions.
Performance monitoring: Monitor robot performance using monitoring tools and key performance indicators. Analyze data to identify opportunities for improvement and adjust parameters if necessary.
Change Management and Continuous Improvement
The integration of collaborative robots can lead to significant changes in production processes and employee roles. It is important to manage these changes proactively and encourage a culture of continuous improvement.
Advice :
Change Management: Clearly communicate the objectives and benefits of robot integration to employees. Involve them in the process to gain their support and facilitate adoption.
Encourage Continuous Improvement: Foster a culture of innovation by gathering feedback from operators on robot use and looking for opportunities to improve processes and performance.
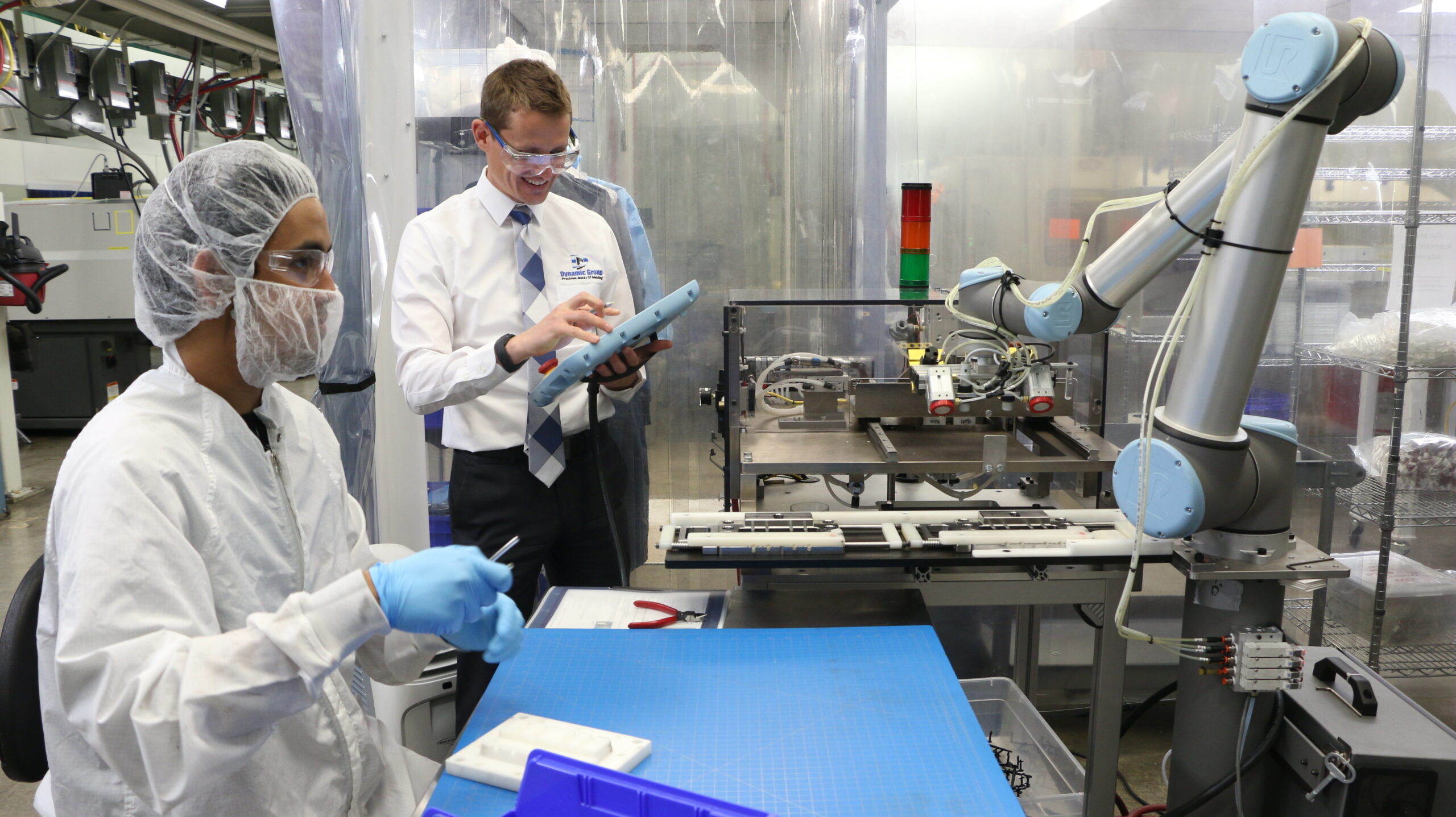
Conclusion
Successfully integrating collaborative robots into a production line requires a thoughtful and strategic approach. By carefully assessing your needs, selecting the right robot, planning the integration, training staff, programming and parameterizing the robot correctly, and ensuring ongoing maintenance and monitoring, you can maximize the benefits of this technology. The integration of collaborative robots offers not only gains in efficiency and quality, but also an opportunity to modernize your production processes and boost your competitiveness in a constantly evolving market.
Do you need advice?